Reverse Engineering the Bookfield Renewable Power Plant
Project Description
Brookfield Renewable Power contracted ECM to conduct a very unique on-site reverse engineering project at their Bear Swamp Generating Station in Western Massachusetts. Bear Swamp Generating Station was developed to deliver supplemental electricity during periods of peak loads – periods when consumers place the heaviest demand on electricity. Completed in 1974, the Bear Swamp complex is a pumped-storage, hydro-electric underground power station that lies along the Deerfield River. With a natural reservoir atop a mountain and a river flowing at the base, the energy potential for this coincidence of nature was remarkable. Deep within the mountain is Cockwell Station, a highly-automated hydroelectric plant that uses a very unique method of generating electricity.
During peak demand hours, the station operates as a conventional hydroelectric generating station. Released from the 118-acre upper reservoir, 10,760 cubic feet of water per second is channeled through a series of tunnels and vanes to drive two turbines, then flows into the lower reservoir. Operating in unison, the two turbines produce a total of 600,000 kilowatts of power that is delivered to the New England power grid.
At night, when energy demand drops, the turbines are reversed and become 415,000-horsepower motors that pump 8,800 cubic feet of water per second 770 feet from the lower reservoir back up into the upper reservoir until it is needed for the next peak period.
The Problem
Bear Swamp needed to replace their current turbines & generators with higher capacity equipment. Since no CAD models or drawings existed for these turbines, ECM was brought in to scan the wicket gates and generate 3D models of the turbines in their as-built condition. These models could then be used in the design and construction of the newer turbines & generators to optimize water flow and therefore create greater amounts of electricity in a cleaner, more efficient manner.
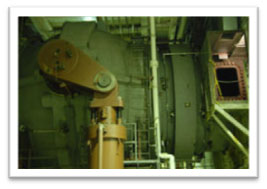
The Solution
With the short amount of time to complete the project it was absolutely critical that the needed measurements were taken efficiently and accurately. In order to get the job done, ECM used the FARO Laser Tracker. The FARO Laser Tracker is an extremely accurate, portable contact measurement system that uses laser technology to perform measurements. The tracker uses a laser distance meter and two rotating axes to track the exact position of a mirrored spherical probe that is guided along the object to be measured. The laser beam is reflected back to a position sensing device that then drives the servo motors in the laser tracker. This closed loop system enables the tracker to follow, or track, the reflector at 1,000 updates per second. The software then stores the measurement values and compares them with CAD data
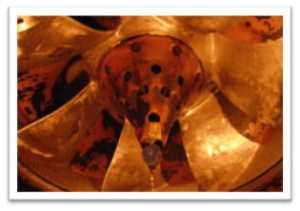
The Outcome
With the accurate data provided by the FARO Laser Tracker, the Bear Swamp Power Company will now be able to bid out the contract for an upgraded turbine runner and generator. Consequently, this new equipment will increase Bear Swamp’s capacity in the provision of low-cost power throughout New England. Normally this complex project would have been extremely difficult & time consuming to complete. However, using the laser trackers with high accuracy, efficient data capture and resiliency within extreme temperatures allowed ECM to finish the job within Bear Swamp’s scheduled downtime.
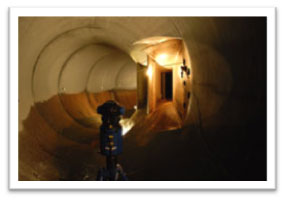