Local Alignment Company Helping to Cure Cancer
Project Description
ECM – Global Measurements Solutions (ECM) of Topsfield, MA is working with ProTom International (ProTom) of Flower Mound, TX to install a state-of-the-art proton therapy treatment center in Flint, Michigan for McLaren Healthcare. This is the first in a series of proton therapy centers to be built by ProTom around the world for treating cancer patients. The healthcare industry is rapidly embracing a new form of radiation treatment termed “Proton Therapy”. Proton Therapy is a blending of particle physics and oncology. It is defined as “a type of particle therapy which uses a beam of protons to irradiate diseased tissue, most often in the treatment of cancer”. This form of treatment has two distinct advantages over traditional x-ray (photon) radiation treatments: lower risk to surrounding tissue due to a highly accurate delivery method and the ability to administer high dosages for specific tumor types. The key to the effectiveness of proton therapy is the accurate positioning of the key components that accelerate, position and deliver the beam of protons to the patient.
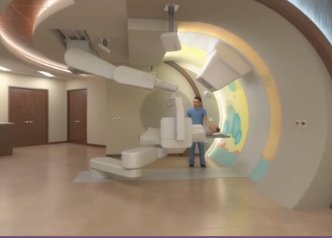
Figure A below depicts a patient on a patient positioning robotic arm preparing to receive proton therapy.
The Problem
ECM was contracted by ProTom to perform the high accuracy alignment of the key components in their proton therapy center under construction in Flint, Michigan. ECM is recognized as a world leader in high accuracy alignment. ECM uses the latest equipment and techniques for inspecting and installing critical components for a wide range of customers in industries ranging from healthcare to aerospace to energy research.
The Solution
ECM was able to support ProTom by providing a solution that featured portable measurement equipment, including laser trackers, digital levels and laser scanners, as well as the most sophisticated measurement and analysis software on the market. ECM worked closely with ProTom personnel to design and implement an inspection and alignment plan that met their exacting requirements and an aggressive installation schedule of all the key components at the Flint, Michigan facility. The initial alignment task required ECM to measure the as-built structure of the concrete building and identify the best alignment in three dimensions for the path of the proton beam. The measurements of the building were performed using a total station and a laser tracker to establish the optimum location for the proton accelerator, switchyard magnets, patient treatment rooms including a 50 ton gantry and the control network used to relate all the key components into one global reference system.
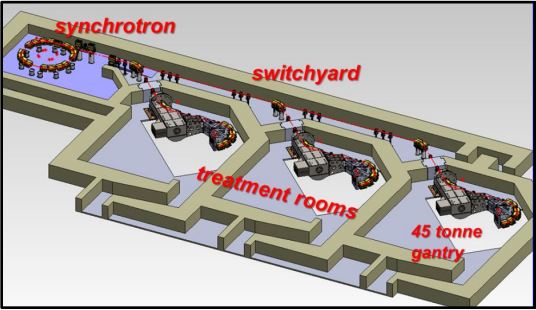
Figure B provides a general layout of the treatment facility with the key components.
Using the as-built measurements of the building, ECM engineers were able to establish the best location for the project origin (X=0, Y=0, Z=0) to relate the installation of all subsequent components along the proton beam path. With the project origin selected, ECM placed approximately 50 reference monuments throughout the facility that would permit ECM to position components within a given area without direct line-of-sight to the project origin. The reference points were valued using a network of several laser trackers to achieve an accuracy of 0.050 mm (2 sigma) over an area approximately 100 meters by 50 meters. This level of accuracy was necessary to ensure that the project tolerances for all the critical components would be achieved.
In planning the measurements for the reference system, ECM engineers performed a software simulation to validate the survey plan prior to conducting the data collection. This simulation was useful in determining optimum line-of-sights to meet the project requirements. In certain instances, openings were fabricated between various rooms to facilitate lines-of-sight that would otherwise be impossible through the 5 ft concrete walls that isolate each of the three treatment rooms from each other. With the project control in place, the next phase of the project was to install the proton accelerator or “synchrotron”. The initial testing of the synchrotron was actually performed offsite in Middleton, Massachusetts at the Bates Accelerator Center prior to the completion of the proton therapy center.
ECM engineers went to Bates and measured the synchrotron to document the original configuration prior to the accelerator being moved to Flint, Michigan. Once the synchrotron arrived in Flint, ECM used the baseline data to install the synchrotron in its final location. The critical aspects of alignment for the synchrotron were its height relative to the gantries, its cylindrical geometry and the rotational clocking of the magnets to ensure that the extraction point was aimed down the center of the switchyard beam hall. If the clocking or height were incorrect, the other components would not be in their proper location resulting in interference with the concrete walls or floors. This would lead to expensive rework of either the building or the previously installed components.
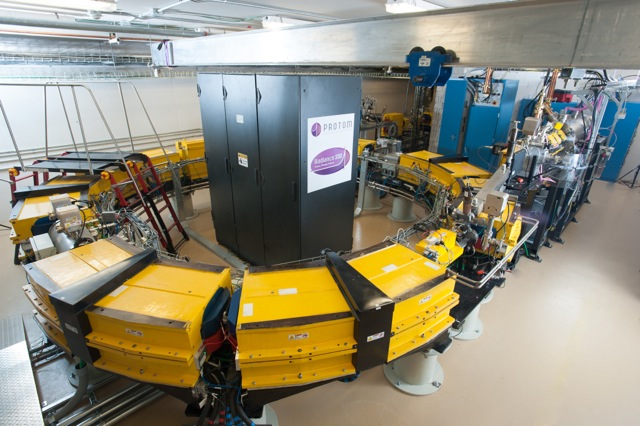
With the synchrotron anchored in place and verified, the next phase required ECM to align the magnets that steer the protons into one of three treatment rooms. This area is referred to as the beam hall or switchyard and requires that the beam be straight and level as well as aimed into each of the three treatment rooms at a specific distance from the synchrotron. Since the concrete floor work is considered “rough construction” and was likely set to +/- ¼ to ½ an inch, the magnet stands required adjustment for floor variations as well as alignment to meet beam straightness requirements. ECM engineers aligned approximately 24 magnets and magnet stands, ensuring that the centerline of the magnets were collinear and that each of the three magnet switch positions were properly aimed toward the corresponding treatment room at the appropriate distance along the beam line.
Once the beam line steering components were set in the switchyards, the next phase required that the proton beam be positioned to enter each treatment room and travel along the spine of the 50 ton gantry steering mechanism. The treatment room alignment had 3 key requirements: the beam must be at the same height between each room, it should make a 45 degree angle with the switchyard beam line and the center of each of the three gantry systems should be equidistant from the switchyard beamline. This symmetrical installation required careful analysis of the existing building concrete work to assess which walls and floors were going to most influence the standardized position of the gantries and beam steering magnets within the treatment rooms.
Using a sophisticated 3D CAD software program, ECM engineers were able to analyze the as-built concrete features of all three treatment rooms simultaneously and identify the correct alignment that minimized construction variations in the building and optimized the proton beam position to meet the demanding requirements for position and symmetry. This analysis was then used to determine the 3D mounting positions for all the critical wall attach features for the 50 ton gantry plates in each room. ECM then worked with the rigging crews to position and align the mounting plates and gantry components in each treatment room.
The final alignment task required that ECM measure the patient positioning system (PPS) which is a robotic arm with a treatment table that coordinates its movement with the gantry to ensure the patient is located in the proper position and orientation relative to the proton beam for optimum results. This is where all the critical alignment work comes to its ultimate conclusion by having the beam of protons arrive at the right location to provide the highest order of effective treatment for the patient. The angle and depth of the peak of the proton beam intensity are critical to ensuring the oncologists are achieving the desired results. This is why the accuracy of each component along the beam path is critical to the final results for the proton therapy.
The Outcome
ECM was able to successfully meet the rigorous accuracy requirements and the demanding schedule constraints for the proton therapy center installation. Several factors were crucial to this success: experience, focus on quality, teamwork and high quality equipment and software. ProTom demonstrated both great faith in ECM and a strong commitment to delivering a quality project. The results of these attributes will be increased cure rates for patients visiting the proton therapy center in the coming years.