By Eric Rosenberg, Metrology Engineer – ECM Global
Applications for large volume laser scanning projects are growing each and every day. The ability to capture large amounts of spatial data of the surrounding territory is quickly becoming a standard project deliverable across a variety of industries. Between the affordability of the equipment, the relatively fast learning curve, and straight-forward post-processing software; companies are recognizing and capitalizing on this exciting technology. This article will dive into the uses of large volume laser scanning both from my personal experiences and ones others are doing. In addition, a terrestrial laser scanning strategy guide will be discussed detailing the ever changing advancements being made to laser scanners and their operation. These changes make it pivotal for laser scanner operators to understand and familiarize themselves with the technology. In such a competitive industry, it will ultimately come down to understanding the laser scanning market and making well educated decisions when trying to advance your large volume laser scanning business.
Introduction
Architecture, construction, power generation, medicine, marine, and law enforcement are some of the industries included on the list of large volume or terrestrial laser scanning applications. Having had the opportunity to undertake scanning projects in the aforementioned industries, I developed the idea that laser scanning can be implemented into almost any project. When done properly, this process can produce data that will help teams better understand project conditions. This article will highlight the uses and help answer questions such as: Is laser scanning right for my project? What are the potential outcomes of large volume/terrestrial laser scanning? I have a point cloud…now what? Included in the article will be the uses of large volume laser scanning and also the deployment and correct operation of terrestrial laser scanners.
Project Background
There are several different terrestrial laser scanners with large volume capabilities available on the market today, each of them containing different features and characteristics to obtain data. The types that will be focused on will be ones using phase shift or time of flight laser technology and are used in static scanning situations. Although kinematic, mobile and UAV-based laser scanning setups allow for large volume data capture they will not be discussed in this article since those forms deserve attention in their own respects.
The capabilities of this powerful measurement tool allow us to capture spatial data points within a 360 degree field of view and ranging 2 feet to 1,000 feet from a single position. Typical file sizes of the data produced from these scanners can range from 1 GB to 100 GB. The millions of data points recorded by the scanner are computed using 1 distance measurement and 2 angular measurements which make up a point cloud. The point cloud is the result of millions of XYZ data points resembling a cloud.
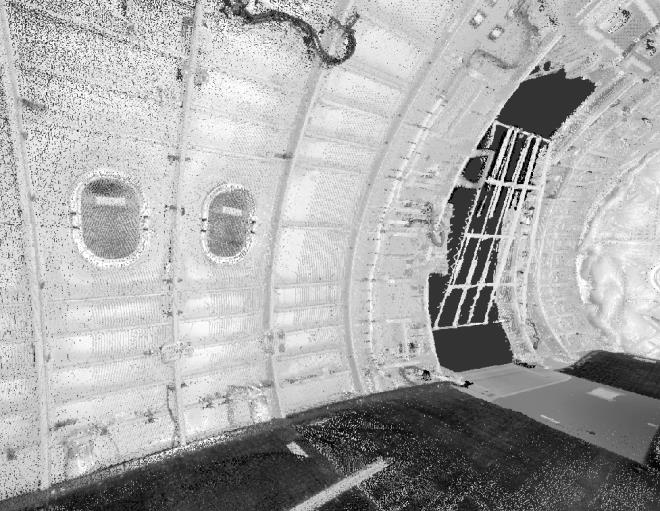
Figure 1: Point cloud of the interior of an aircraft fuselage. Millions of data points combine to what appears to be a 3D model.
The distance measurement is recorded by the laser either using phase shift or time of flight sensing. Phase shift scanners emit a known phase based laser beam and by sensing the difference in the reflected phase, a distance is calculated. Time of flight scanners use the precisely known value of light-speed and a sensor that detects the time elapsed from emission to detection of a pulse based laser beam.
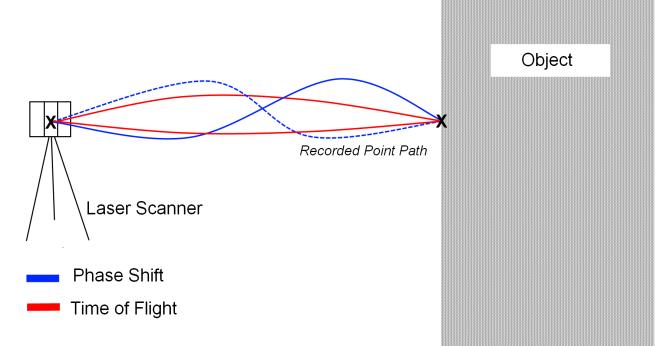
Figure 2: Visual representation of the laser beam path as it records a data point.
Both technologies primarily dominate the large volume laser scanning industry because of their ability to maintain accuracy at high data acquisition rates and long distances. Prices for a new scanner with large volume capabilities (360 degree field of view, range greater than 250 feet) are typically between $40,000 to $100,000. Prices vary depending on several technical specifications like accuracy, resolution, effective range, and data acquisition speed. In addition, other advancements are being implemented to increase workflow like internal cameras, wifi connectivity, built-in data storage, and longer battery life. As mentioned earlier, terrestrial laser scanners can be integrated into a kinematic, mobile, or an UAV scanning assembly.
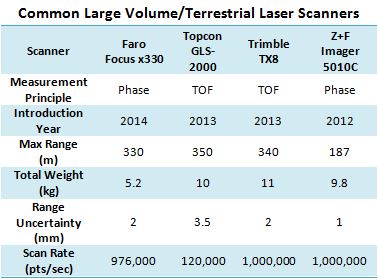
Table 1: Comparison of key features available on common terrestrial laser scanners.1,2,3,4
Application and Uses
The global 3D laser scanning market is expected to double over the next 5 years according to the research firm MarketsandMarkets 5 with the main driver being the need to improve project efficiency. What a two-man crew could capture in a day’s work without a laser scanner is now being done with just one operator, coming away with a fully digitized version containing millions of data points. Terrestrial laser scanners have become the go-to tool to capture existing conditions of just about any project site. The ability to digitally document sites is being widely used in industries like construction, shipbuilding, and facility maintenance.
Construction and architectural professionals are capitalizing on the use with the rapidly evolving BIM community (Building Information Model). Never before have project managers had more access to their sites with the help of point clouds which can cover all areas of the job site allowing for easier management and safer protocols by understanding site conditions right from their office. Entire facility renderings can be produced of all existing building geometry.
Being able to measure existing conditions has been especially useful in the marine industry. Ships can be checked to original specifications and monitored for more accurate and efficient maintenance programs. Comparing a point cloud produced from the laser scanner to original CAD models is now the preferred method to check surface deformation. Large volume inspection has saved a lot of time and money for various manufacturers such as those making airplanes, trains, and ships where surfaces can become quite complex.
Since point clouds only contain spatial XYZ data, it is sometimes necessary to convert point cloud data into CAD models. Teams can capture existing conditions and produce models in order to create newly integrated designs such as in the case of complex piping networks and building remodeling.
However, in numerous cases, laser scanning projects start and end with the creation of a point cloud. This data set contains exact measurements and displays of whatever the project site was at that time. Uses in facility management is increasing due to the fact that inventory can be accurately and properly controlled as well as aiding in site visualization. Law enforcement is implementing scanning into their forensics departments for purposes of full crime scene documentation. Site planners with large volume excavation and stock piling businesses now have a safer method for their inspection procedures. With many of the scanners having embedded GPS and inclination sensors, land surveyors are gathering far more geo-referenced measurements than ever before. Most post-processing software contains various measurement tools that allow the user to better understand their point cloud. The ease and simplicity of being fully immersed in your project at all times makes laser scanning the right choice in most large volume professional applications.
Laser Scanning Strategy
A scan typically ranges from 2 minutes to 30 minutes depending on the density, sampling, and field of view settings. Some scanners are able to record a panoramic photograph which is superimposed onto the point cloud resulting in colorized RGB data points. Each point cloud created does not have any positional reference to the other scans. In order to reference several scans together, software will require using targets or in the case that targets aren’t used; the scans overlap each other. Each scanning technique will result in an accurate and full point cloud, however, only the use of targets will ensure accuracy maximization. Common targets include spheres and checkerboard patterns. Spheres allow for detection at limitless angles, whereas checkerboard patterns shouldn’t be relied on at line of sight angles greater than 45 degrees. In the case of scan registration, a minimum of 3 targets need to be detected in order to reference other scans in the data set. A target-less laser scanning project should have between 50% – 80% overlapped data and clear sights at common planar features (walls, floors, ceilings, etc.) To limit error potential, it’s useful to know that registration algorithms prefer 3 axis of constraint for example intersecting walls and the floor.
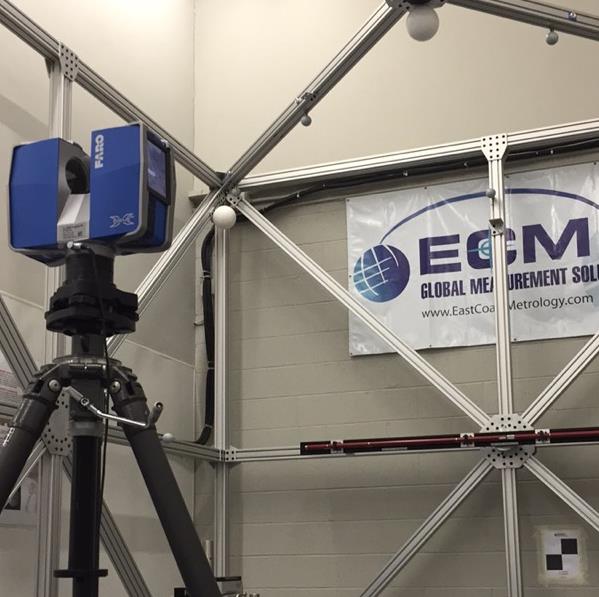
Figure 3: Faro Focus x330 shown with common scanner targets.
It is recommended that the measurement plan should include a scan designated as your “master scan”. After a preliminary site walk-through is performed, the operator should pick an area that has multiple lines of sights to different areas of interest, a view of multiple levels, and a view of as many common targets located in different areas of scanning interest. The first scan of the data set should be taken here since this will have all additional scans branching off. Using this method will strengthen the target accuracy and will allow for an easier and smoother registration workflow. An example of an area that would make for a good master scan location would be the atrium of a building where the scanner scan see multiple interior building levels and also measure targets at several different areas of interest all from one position.
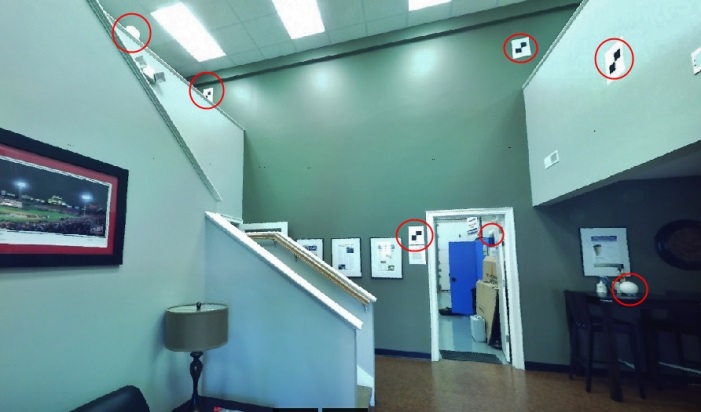
Figure 4: Scanner photograph of a master scan location, with targets circled in red.
The ability to capture massive amounts of data can sometimes be more cumbersome to a project than helpful. Most scanners on the market allow the user to alter resolution and sampling settings which in turn impacts the time and ultimately the file size. Since completed data sets can reach upwards of 100GB for an entire point cloud, managing file sizes is crucial. The resolution settings directly impact the density of the point cloud, therefore a higher resolution means more points which means more scanning time which means larger file sizes.
Having a solid idea of what is expected for the project deliverable will help in adjusting the resolution settings accordingly. An example would be if the assignment was to just capture basic building geometry (doors, windows, walls, etc.) then a low dense scan can be used since all that is needed is just sparse coverage of objects in order to obtain basic dimensions. Whereas in the case of a preparing a point cloud for modeling purposes, the resolution settings should be set to high since extra detail will be required in order to produce accurate models.
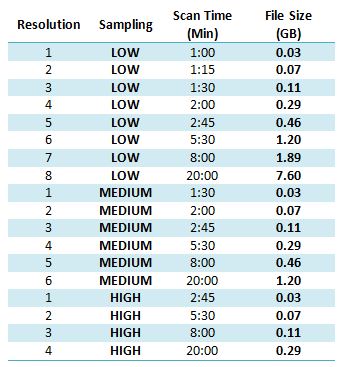
Table 2: Various scanner settings displaying the exported point cloud file size in ASCII.xyz format. (Note: Resolution values indicate 1 = lowest, 8 = highest setting)
The other main setting that can be adjusted is sampling which controls the frequency that a single point is measured creating less false readings of data points. This false reading of data points is referred to as “noise”, which can be affected by the reflectiveness of measured surfaces and/or distance. A higher sampling setting will produce a more defined point cloud as well as a smaller file size since there are not as many extraneous data points recorded; however, time spent out in the field is significantly greater.
Discussion and Findings
Many variables can occur that will affect data quality and time spent out in the field. The skill in knowing how different variables will affect the data typically comes with more scanning experience; however, all outcomes can usually be predicted beforehand with proper understanding.
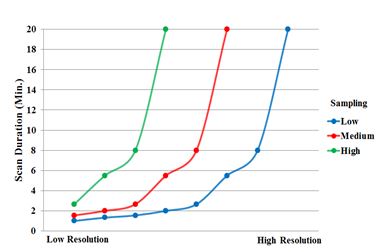
Table 3: Graph showing the impact of increasing point sampling and its effect on scanning time.
Terrestrial laser scanners are extremely useful because of their versatility; the most likely projects for adverse conditions are ones taking place outdoors. Most scanners have settings and/or filters to deal with outdoor conditions like sun light, distant objects, and sky conditions. Typically, working during direct sunlight hours is not recommended, doing this creates “noisier” point clouds which require more extensive post processing clean up. Also inclement weather should be avoided (wind, snow, and rain) since data can be corrupted due to movement of the instrument. Improvisation and creativity will often help in gathering data when needed, such as ensuring the stabilization of the scanner using counter-weights.
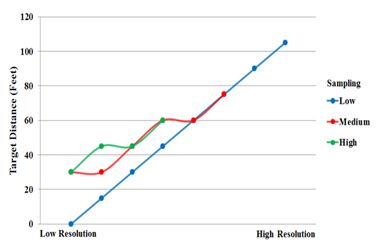
Table 4: Graph showing ability to measure targets at different scanner settings.
Performing an entire project on a single scan setting is not always the most efficient method. For example, scans that require long distance capture of targets, the operator should be aware of which setting gives them the best chance to capture those targets. Whereas scans with the sole purpose of preventing “shadowing” or filling in scanner blind spots should have a different setting.
When considering whether or not to deploy a terrestrial laser scanner, it helps in knowing what has been scanned and what has not. Each available scanner has options to customize scan settings and this versatility allows for project creativity. The potential and on-going uses of large volume laser scanning are being taken advantage of in your industry and being well-informed will help drive a successful scanning business.
ACKNOWLEDGMENTS
Helpful insight into the creation of this article was provided by co-workers at ECM Global and other colleagues in the industry.
REFERENCES
- Faro, Faro Laser Scanner Focus X330 Features, Benefits & Technical Specifications, October, 2013.
- Topcon, GLS-2000 Compact High-Speed 3D Laser Scanner, August 2014.
- Trimble, Trimble TX8 Laser Scanner Datasheet, April 2015.
- Z+F, Z+F Imager 5010C Technical Data, February 2013.
- Marketandmarkets.com, 3D Scanning Market – By Devices (Optical, Laser, Structured Light), Range (Short, Medium, Large), Solutions (Portable, PCMM), Services (Reverse Engineering, Quality Inspection, Rapid Prototyping) – Worldwide Market Forecasts and Analysis (2013-2018), July 2013.