Whether its online ads, blogs or webinars, Digital Twin is the latest term to permeate the AEC and facilities industries. What exactly is a Digital Twin?
Article by John Smits, VP-AEC Division – ECM Global
Is it a fancier name for Building Information Modeling, commonly known as BIM? Do you need 3D Laser scanning to construct a Digital Twin? More importantly, how does a Digital Twin or BIM lend value to facility operations and construction projects?
BIM began as a means to coordinate the various disciplines of construction documents. It enabled multiple designers across different disciplines to see how their designs interact with others, all in a true scale 3D environment. The software automatically generates schedules, lists of building materials and systems. The use of BIM altered the way buildings are designed, placing more time and effort in the design phase, while reducing time in the construction document phase of a project. This process created construction documents that accurately depicted how various building systems would interact. Clash detection between items such as structural members and MEP systems were resolved early on, rather than during construction. This led to faster construction times with less change orders, creating more value for the owner. As an added bonus, the owners also received a 3D digital model of the building for use in future renovations and maintenance.
The BIM model is essentially a Digital Twin; it is a 3D digital depiction of all the parts and pieces that make up a building. But what about the furnishings, equipment, the various systems such as lighting, fire suppression and energy management? What about the people who populate the building and their use of the spaces?
The need to integrate both the use and workings of a building into BIM models is what led to the concept of a Digital Twin. More than just a scalable image of the building, the Digital Twin is a cloud-based repository of a smart building’s data that is generated from a multitude of constructs, devices and sensors. A BIM model is often an essential part of that data as it provides the parameters within which all the systems operate. This data in turn allows management of assets, space or personnel within the building via simulations.
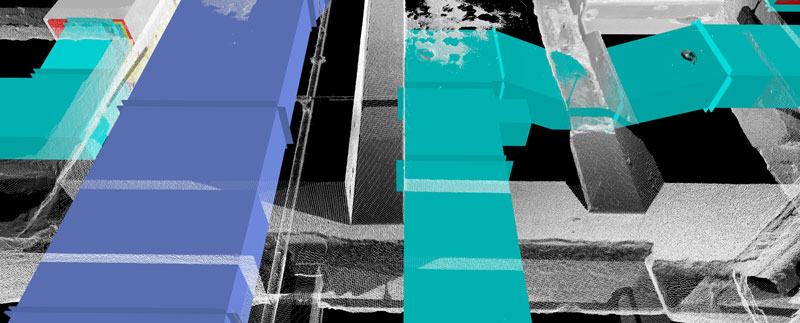
BIM essentially started in the late 1990s. CAD technologies were developed using 3D parametric modeling and integration with information management systems was added soon thereafter, leading to the creation of BIM. By 2001 BIM had taken a firm hold within the AEC industry as design documents shifted to 3D imagery. However most facility and operations managers are currently working within older facilities that predate that technology. Their building data is not a BIM model but a bin of 2D blueprints, documents that often are not true representations of their facilities’ current condition. So how does one efficiently create a 3D model of these older buildings?
3D laser scanning has become a proven method to solve that problem. By scanning the interior and exterior of an existing facility with modern 3D scanning technology, a true to scale digital representation of the building is created. The resulting digital scan data can be used as a standalone within various software that adds information management, tags and schedules for various systems, fixtures and parts within the building. The data can also be used to construct a 3D CAD model of the facility, forming an accurate and precise 3D digital base for planning renovations, modifications and maintenance to the building or its equipment.
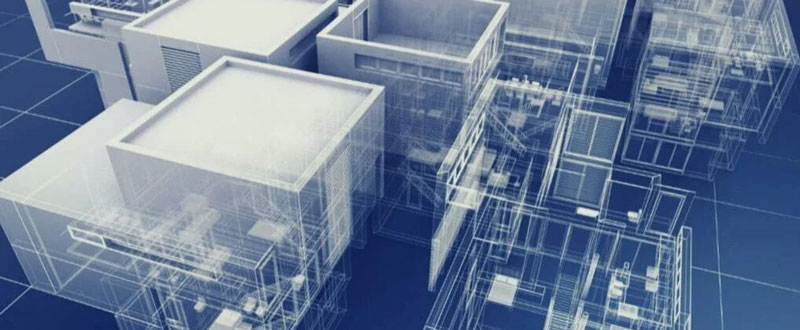
When making a decision to employ 3D scanning technology, the type of equipment and scanning methods used are crucial. Depending on the size of the facility, controls and targets may be needed in order to allow for precise planning for renovations. If the facility has large amounts of mechanical equipment and machinery that needs to be documented, a mixture of hand scanning and medium range scanners may deliver the best results. Permanent survey controls can also be installed throughout the facility, setting up a geo reference grid within the facility that may be used for construction as well as future updating of the 3D model. High precision scanners such as laser trackers can be employed during construction to provide accurate installations of sensitive equipment and pathways for conveyor systems.
Scanners vary in their precision and data quality; a skilled experienced technician will know how to use the right scanner and process to achieve the desired deliverable. ECM is an industry leader recognized for our BIM capabilities and skilled engineers. Our scanning services and 3D Models offer you the benefits of:
- Up-to-date representation of your facility
- Accurate design planning base
- Shorter construction timelines
- Reduced materials waste
- Increased safety and reduced risks during operations
Whether you are contemplating a modification to your production line or need a full scale 3D model of your facility, ECM will offer you a cost-effective solution with an accurate deliverable as an important first step in creating your Digital Twin.