Project Description
In greater Downeast Maine, boat builder Hodgdon Yachts plan for the construction of the 100 foot racing yacht New^3 (also known as New Cubed.) Set to be constructed and finished towards the end of the year, the vessel will be shipped to Australia for its first race. Tim Hacket, the project manager and coordinator, explained, “We spent a lot of time planning the construction of each part to ensure everything is built in time for its final installation into the hull or onto the deck.” Hacket’s job is to ensure the composite yacht is constructed with the best methods at the highest quality while remaining as lightweight as possible. “Brandon Linton, the lead, and I have used East Coast Metrology (ECM) for two similar projects in the past with great results.” Hackett said. ECM was responsible for taking precise measurements during multiple phases of the hull plug construction.
The Problem
There were three big obstacles with this shipbuilding project: Time frame, skilled labor and supplies. The time frame for ship construction is short, suppliers need to deliver boat building materials in a timely manner and boat builders with composite construction experience (honeycomb with carbon pre-impregnated with epoxy laminate construction) are needed. Considering these fabrication hurdles that are apparent in just the initial stages of the planning, Hodgdon Yachts must work in lead times with suppliers and then coordinate drawings and deliveries that specify materials needed. In the case of the New Cubed honeycomb core, there is a lead time of up to 20 weeks for manufacturing and delivery. Therefore, Hacket and his team rely on advance coordination and project management techniques to juggle each task.
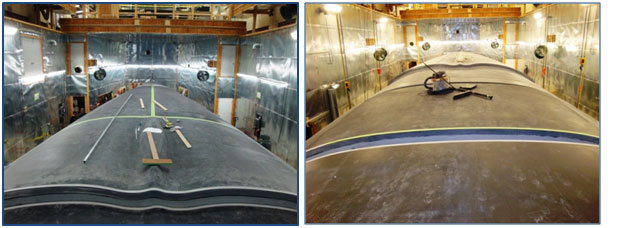
The Solution
With ECM metrologists able to come on-site to capture the hull plug shape and measure the distance between end points and mast head, the management of these challenges became easier. East Coast Metrology technicians often work on-site without much customer direction and within a tight timeframe. Fitting custom measurements into a limited window of opportunity is exactly what ECM specializes in accomplishing for clients.
The Outcome
ECM got to work at the East Boothbay, Maine location, using a laser tracker to gather highly accurate hull shape data at the boat yard within a very confined area.
During the pre-assembly stage, ECM technicians first inspected the individual hull plug pieces to ensure all pieces were within tolerance. The surface of the hull plug was scanned, collecting real-time 3D dimensional data, to define whether or not the shape of the hull harmonized with the hull design intent. A technician checked for flexing in the bow, verifying key dimensions relative to the drawing. Measurement tolerances for racing yachts allow for little if any building errors, so any deviations from the design intent were corrected or at least communicated to the customer. The laser tracker was positioned around and on the male mold to check angular distance and to take advantage of the hulls unique shape.
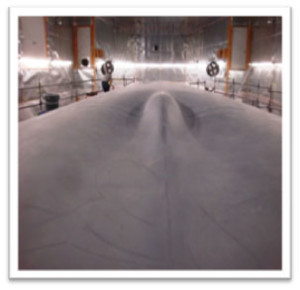
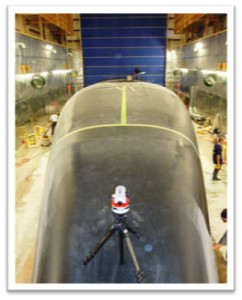
“With this project and the ones in the past, ECM has worked with us to deliver well-constructed boats [built] to a high standard, on time, within budget and light weight. This is always a challenge as most parts are custom made,” explained Hacket.
The Hodgdon Yacht team advises to “One: Plan well, Two: Choose a good team of people around you with years of building experience, Three: Use good metrologists. A boat has such a complex shape and metrology is the only real way to check the surface accurately and quickly.” Following this sequence highlights ECM’s reliable measurement services.
“With using ECM we can check over the CNC milled parts to ensure they are as close to the designed surface as possible. The scanning of the hull plug saves many days’ worth of work in only a few hours and the same goes for when the hull mold is setup and finally when we have to mark out the entire structure of the boat.” Proper measurements ensure the hull will not crack during the race, which acts as peace of mind for the racing team.
“This job normally would take 3 to 4 people a week and with ECM the same is achieved in a day.” ECM is an excellent choice for measuring advanced composites and high performance racing and cruising boats.
– Tim Hacket, Design and Build Team Coordinator / Project Manager at Hodgdon Yachts, ECM’s main point-of-contact for boat equipment suppliers and boat manufacturers