The Problem
Veteran bowler, Ralph Dahlgren, wanted to replicate a favorite bowling ball that had the “perfect grip” for his right hand. He purchased 8 additional bowling balls from a trusted manufacturer and delivered them to a professional bowling ball machine shop to match the existing, ideal bowling ball grip pattern. However, after receiving the customized bowling balls and practicing with them, Ralph discovered that not one ball felt the same and his bowling suffered because of the variation in his release based on the differences in the grip pattern.
To consistently release the bowling ball, Ralph needed the holes drilled into the ball to be identical in spacing, angle and size. He had the pro shop double check their work and they assured him that each ball was identical to the ideal bowling ball he provided. Frustrated, Ralph turned to East Coast Metrology (ECM) to measure the bowling ball grips using high accuracy metrology techniques to resolve the problems he was experiencing. Ralph has worked with ECM on many of his projects for his day job, so it was natural to use ECM to help resolve this disparity. “I have used ECM’s precision measurement services for over 20 years to verify compliance of many very complex geometric shapes as it relates to the medical equipment, semiconductor equipment and defense industries. Certainly mapping holes in a sphere was well within their capability.”
The Solution
Ralph provided ECM with his preferred bowling ball and the 8 new, customized grip bowling balls. ECM elected to use a PCMM arm to measure the holes, including their relative location, angle and any taper or ovality in the grip. The choice to use a PCMM was based on the need to measure inside the holes, which can be difficult with other high accuracy metrology technologies, such as laser trackers or laser scanners, due to the highly restricted visibility and access to the finger holes. The PCMM allows the operator to use a longer probe tip to accurately measure any taper in the hole as well as get a better measurement on the angle down to the base of each hole. This is critical to determining why the “feel” of each of the 8 new bowling balls was different to the original.
An ECM technician measured each bowling ball, defining a coordinate system using the center of the bowling ball as the origin, creating an XY plane through the centers of the ball and the two finger holes and clocking through the right finger hole (see image below.) ECM then documented the XYZ locations and shape of the thumb and 2 finger holes at the ball surface, the angle, taper and depth of the 3 holes, as well as the overall ball diameter for each of the 8 replica balls as well as the master bowling ball. This data was then exported for analysis.
The first graph shows the variation in the bowling ball diameters based on creating a sphere from the surface measurements of each ball. The bowling ball diameters are clustered around a fairly narrow band except for the Track920 ball, which is smaller than the others.
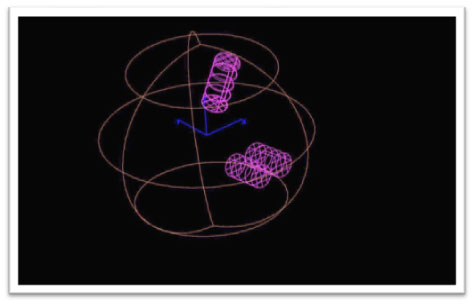
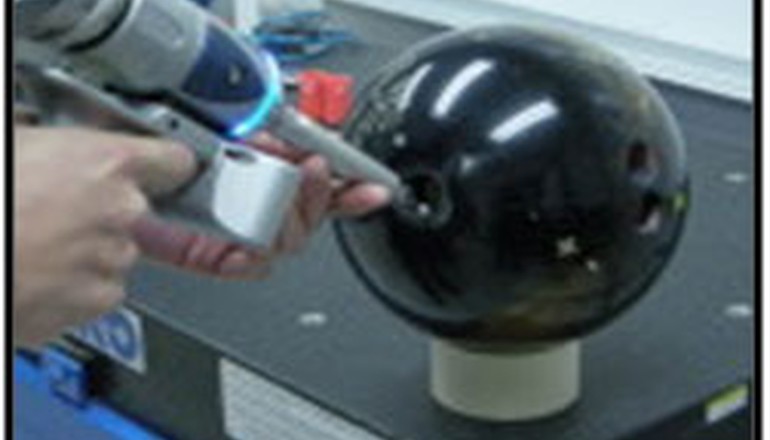
From the measurement results, it is apparent that not only do the original manufacturers of the bowling balls have variation in the diameter of the balls they sell, but the specialty bowling shop that customizes the grips by drilling holes that should match the “perfect” ball, Anarchy, can’t reproduce the grip dimensions either in diameter or depth. Additional analysis on hole angle would likely reflect errors in alignment of the holes relative to centerline.
The Outcome
Ultimately, the 3D scanning ECM performed on the bowling ball showed that, “Bowl shops can’t drill uniform holes so what is produced in a bowling ball can’t be replicated.” Ralph Dahlgren’s goal of achieving high accuracy grip replication requires greater accuracy on the part of the bowling pro shops. Traditional drilling techniques and accuracies are not sufficient for the highly skilled bowler with a keen sensitivity to even small variations in the bowling ball grip.
Ralph Dahlgren
Engineer at Boose Aluminum Foundry
Regional Sales Manager
Bowling Enthusiast