Project Description
To commercial fishermen proper equipment is crucial to making a living. The owners of Atlantic Trawlers understand this well: “We manage and operate 5 offshore fishing vessels where we specialize in the harvest of healthy offshore fish species, like haddock, pollock and redfish,” commented Marty Odlin. Fishing off the Gulf of Maine and George’s Bank, requires durable boats with strong propellers that fight the tides and get the Atlantic Trawler team to the fishing grounds and back to port safely.
The Problem
Atlantic Trawlers has a commercial fishing vessel named Harmony that out performs other boats the same size. It’s known as one of the top fishing vessels in the region, “The boat’s fair lines, powerful engine and propeller allow it to efficiently and effectively harvest fish in vicious tides,” explained Odlin. He felt the propeller was one of the key elements since boats of similar shape and engine horsepower still didn’t have the same performance as Harmony. Unfortunately, the drawback of older ships is they lack drawings identifying the key dimensions. Thus, Atlantic Trawlers was faced with the challenge of recreating the four bladed propeller dimensions so it could be replicated for use on other ships in their fleet. Oldin explained that, “The propeller is over 25 years old. We couldn’t find any original drawings or molds, so we have to make our own.”
Atlantic Trawlers needed an accurate and fast method of measuring the Harmony propeller and generating a representative CAD model of the part. This process is called reverse engineering and is a specialty of ECM Global Measurement Services. The ultimate goal was to develop the CAD model so Atlantic Trawlers could manufacture both a back-up prop for Harmony in case it was damaged and to provide similar props for the rest of the fleet. Compounding matters was the limited access to the propeller during a haul-out of Harmony for routine maintenance. The data collection for the propeller could not delay the return of the vessel to the commercial fishing grounds.
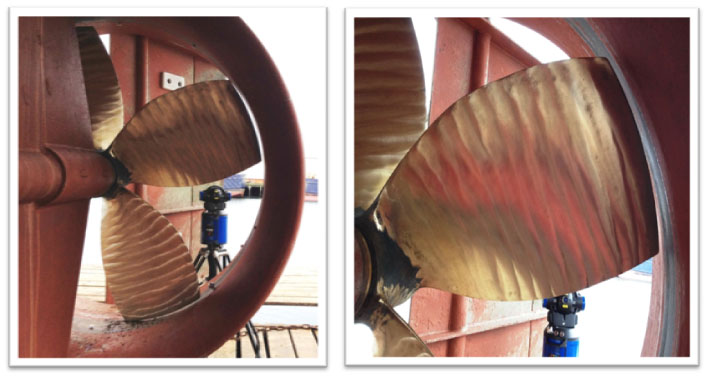
Measurement of propeller to document dimensions for creating a 3D CAD model.
The Solution
Fortunately, Atlantic Trawler’s boat yard was only a few hours away from ECM in Portland, Maine. ECM was quickly on-site with a laser tracker used to measure the propeller within just a few hours. The complex blade geometry was captured and Harmony was released back to the boat yard. The main challenge in gathering the measurements was that the propeller was mounted on the ships drive shaft under the hull. The laser tracker, with its ability to scan points at up to 1000 pts per second, proved to be ideal for the task and is sufficiently portable to fit in the confined area under the hull.
The propeller measurements were then loaded onto a laptop back at ECM and imported into a CAD package that allows constructing features and surfaces from the point data. For this particular case, one of the four blades was fitted with complex surface geometry (also called NURBS surfaces) then the other three blades were just created by rotating the initial CAD rendered blade the 90 degrees until there were four identically shaped blades in the model. As a quality check on the process, the actual measurements for the other three blades are compared to the “engineered” surface of the main blade to look for disparities and any deformation that needs to be considered.
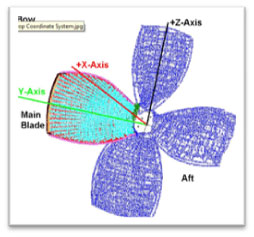
The image above shows the point cloud data for the propeller along with the constructed reference frame located at the propeller center and clocked through the reverse engineered propeller blade. The other three blades show the density of the point data collected to ensure adequate coverage for assessing symmetry to the original blade. In some cases, a client will request that all four blades be reverse engineered, but for Atlantic Trawlers, symmetric blade fabrication was an important goal for the project.
Finally, the propeller model was converted into STL and IGES CAD files with a fully surfaced model from the ship propeller data and delivered to Atlantic Trawlers. This information would then be used to generate CAD based drawings and surface definitions for either creating a mold to pour a replica of the Harmony propeller or to generate a 5 axis NC machine program to machine the propeller from a block of the appropriate metal alloy.
Atlantic Trawlers was appreciative of the quick response of ECM to be able to measure the propeller without causing an interruption in their normal maintenance of the Harmony. The fact that a single company had the resources and skills to collect the propeller data on such short notice, generate the 3D CAD model and provide a quality check on the existing propeller were distinct advantages to the customer. ECM was able to provide low cost reverse engineering and large scale metrology services that satisfied the needs of Atlantic Trawlers.