Taking Roller Coaster Accident Prevention and Maintenance To The Next Level Using 3D Scanning Technology
Project Description
When it comes to amusement park attractions, roller coasters seem to top the list of thrill rides to experience during your visit. But, when you finally step onto that precision engineered attraction you’ve been waiting in a long line for hours to experience, do you think about how it was designed, constructed….inspected? The mechanical design process and assembly logistics that go into these rides is not usually the first thing that comes to mind as you’re stepping onto one. Just like any other large structure, whether a bridge, a plane, or even a skyscraper, there is a lot of engineering work behind the scenes that make it safe for people to enjoy on a daily basis. And safety is an amusement park’s number one priority!
For the past 35 years, Dr. Masoud Sanayei, a Professor of Civil and Environmental Engineering, has conducted research on structural health monitoring of bridges and other structures. By using instruments such as strain gages, accelerometers, tiltmeters, thermocouples, optical sensors, and various data acquisition systems, he is able to collect, measure, and process information that enables him to comprehensively evaluate the condition of these structures.
More specifically, his computer models of existing structures can be subjected to a series of loading patterns within finite element simulations for prediction of structural system responses. The results of these simulation models display how a structure reacts to repetitive cyclical loading from a fatigue perspective. Professor Sanayei and his doctoral student, Sofia Puerto Tchemodanova, are planning to use this data for predicting what regions of a structure may benefit from fatigue loading studies for potential preventive maintenance.
Although a roller coaster is not a bridge, it is still a load-bearing structure; and like a truck, the roller coaster train travels on it, similar to bridges. “We use the data collected for stress analysis and for ultimate human comfort and safety. Most of my research has been on bridges, so much so, that I call myself ‘The Bridge Doctor.’ The same way that doctors put sensors on their patients and get EKGs to evaluate health, I instrument bridges with strain gages, accelerometers, tiltmeters, and temperature sensors. From there we determine the health condition of bridges,” explains Professor Sanayei.
The Challenge
Unlike medical doctors who can utilize various types of tests and equipment to determine the health of their patients, with structures like bridges, buildings, and roller coasters, it is not so straight forward. To determine the health of structures, one must create a physics-based mathematical model to interpret and evaluate the predicted response of the structure compared to its actual measurements. In order to create his diagnostic computer model, Professor Sanayei needed to have the exact geometry and material properties of the roller coaster structure.
Almost all newer roller coasters have digital design files, making it easier to inspect and test on a regular basis. However, older structures might not have such drawings or as-built drawings. Professor Sanayei did not have the required geometry of this particular roller coaster needed to conduct his research. That’s why he partnered with the experienced Engineers at East Coast Metrology (recognized as ECM – Global Measurement Solutions). He also needed the laser scans completed quickly and efficiently, while working around a very rigorous teaching schedule. By partnering with ECM, he was able to obtain an as-built model of the roller coaster in which he could use regions of interest to run mathematical models and simulations. The model was comprised of all the components from the foundation and main support column and connections to the box girder beam, support brackets, and the tubular rails.
In years past, it was uncommon to have a digital design model of the roller coaster to compare to the as-built design. Engineers used blue prints and other hard copy drawings from the architect to make the design a reality. Although newer roller coasters have digital design files, these files often don’t reflect how the structure was actually built or retrofitted during its service life. Roller coasters are constructed in large pieces inside a factory. Those pieces are then shipped to the destination where they are fitted together for the first time. Many times, the pieces do not end up fitting together as originally designed and therefore must be modified to fit into their proper position. This is common for almost any large structure. Because of this, these areas which get altered deviate from the original drawings. In addition, after the ride has been constructed, it has a tendency to settle, creating additional areas of uncertainty. By having an as- built model, Sanayei has full confidence that his simulations accurately represent the conditions in the field.
The Importance of Choosing the Proper Equipment
Based on the scope of the application which consisted of measuring and modeling four box girders and three supporting columns with their attachment gussets (plates that hold the roller coaster down), ECM chose the FARO|Focus 3D Laser Scanner to efficiently capture a widespread area of the roller coaster’s first downfall section. Once the required data was captured, ECM then complimented these scan results by using the FARO|Edge Portable CMM Arm to more accurately conduct a cross-scan of the welded section to create the full digital geometry model of the high stress areas within the research scope. When choosing which scanners to use for the job, ECM had to take into consideration several variables such as size of the structure, area of interest for scanning, distance to the target structure, weather conditions, movements , and accessibility.
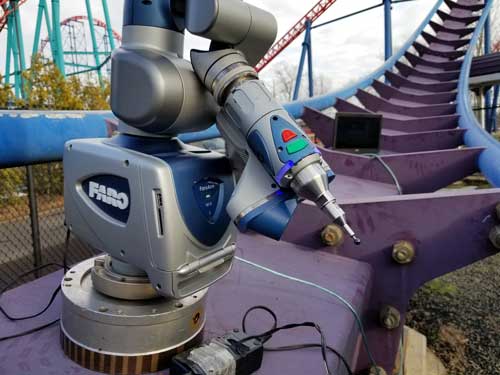
When scanning outdoor structures that are also extremely high, there are always temperature and wind variables to overcome. That, paired with the limitations that technology can have in certain weather conditions, makes it difficult to capture the clean, high tolerance data needed to create the digital model. For this reason you must be very careful when choosing the piece of measurement equipment used for the job.
The Solution
Using magnetic bases to assist in securing the equipment to the edge of the coaster along with a scissor lift to access the top, ECM was able to capture 360⁰ degree coverage of the target sight with a range of 30 meters. The goal was to acquire as much data as possible in a relatively short period of time with minimal noise (excess data that is irrelevant). “It was a challenge getting underneath this specific section of the coaster due to the many bushes and shrubbery and other structures nearby, but we were able to position the scanner just high enough to capture the data we needed without sacrificing quality. In some instances this required more localized setups,” stated Mike DiVito – ECM Engineer.
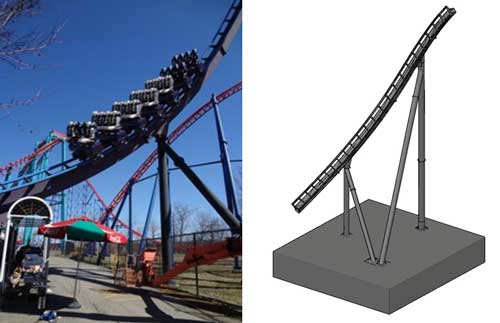
Once the scanning phase was completed, ECM began their post processing phase. This consisted of stitching all the individual scans to one another ultimately creating one large file containing all the point clouds as well as overlaid images. ECM removed any superfluous data (ground cover, surrounding trees, other structures, and noise), then created a polygonal mesh. The final step was to make numerous planes and sketches which are drawn, extruded, or lofted and merged, all making one complete solid model. This is what we call the “as-built” digital model, for it is a full parametric model that is the best representation of the collected metrology data.
For Sanayei’s portion of the measurement testing, all sensors and instruments were calibrated to achieve accurate results; however, the number and type of instruments used along with location depends on what is being monitored. There is an additional need for validation and verification of measurements to make sure everything is working right. By pairing the measurements taken from the sensors and gages with the data collected from the 3D scanning, we are breaking through that barrier to reach the cutting edge of technology. That allows for the section as a whole to be completely verified and accurately monitored moving forward. The ECM model provides a realistic sense of the as-built structure, and not what the design “should” have been.
The Outcome
“This has been a fun project and it is not done, but based on our intermediate analysis, the stresses are way below any level that anyone would have any concerns,” states Professor Sanayei. As anticipated, the roller coaster structure is perfectly safe. This research that was conducted along with the rigorous testing and daily inspections the park adheres to, makes a roller coaster one of the safest ways to experience that thrill you look forward to at amusement parks. “I have great gratitude to the park for allowing me to conduct my research on this project and put my classroom teachings into a reality-based environment. We continue to look at new methodologies for structural health monitoring when it comes to cyclical loading using finite element modeling for fatigue life predictions. 3D scanning technology enables me to capture data above and beyond my original expectations.” – Professor Masoud Sanayei